Clutch outer removal and replacement. I have just done this job without using the Honda 'special tool'.
Gathering other information from this forum I include some pictures of how it can be done. I have started from getting to the point where the covers and drive faces have been removed and you're ready to get stuck in. The reason for this is because there is already plenty of info on this forum and videos on You Tube to get down to this point.
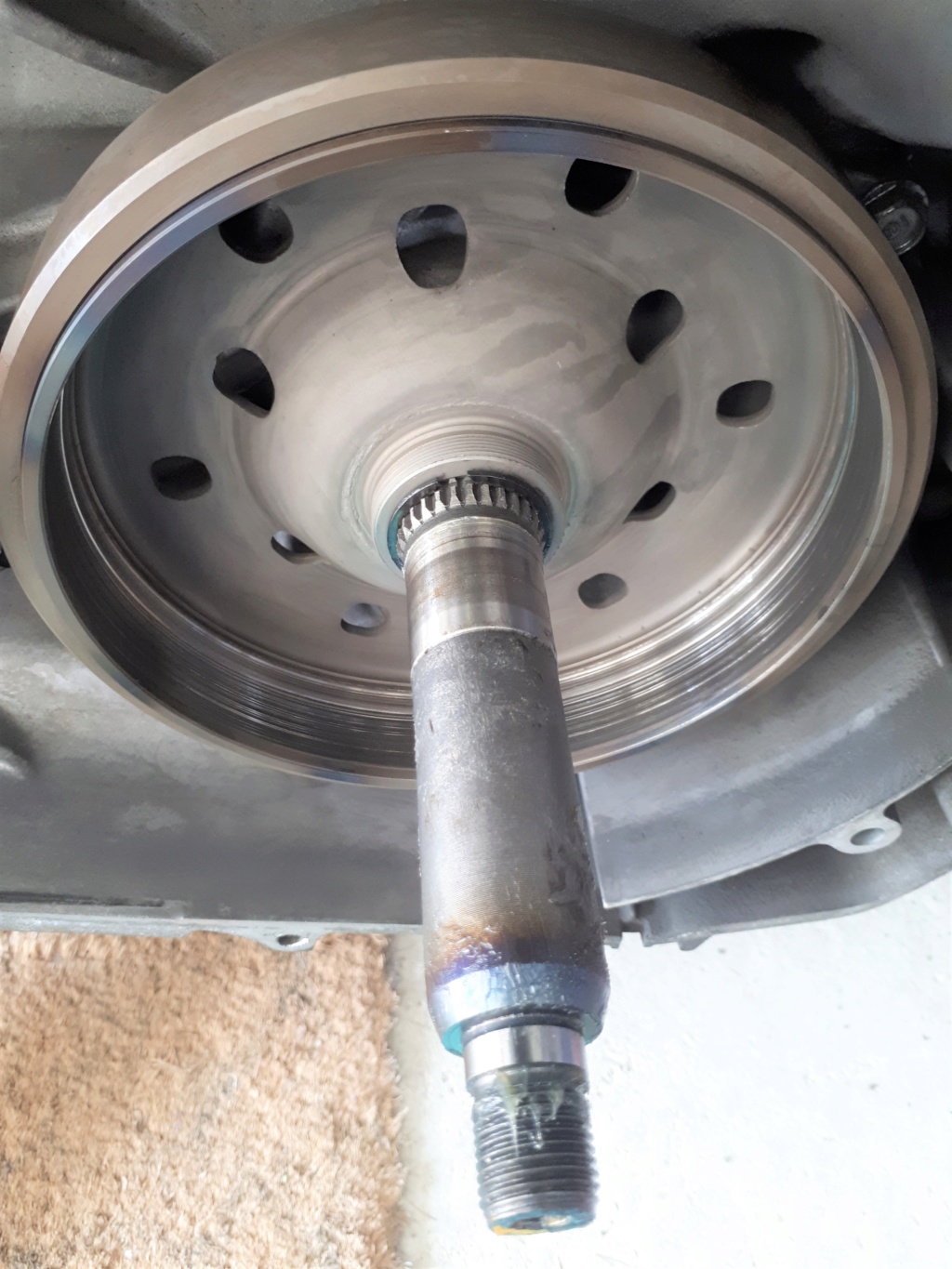
I removed the circlip, which holds the outer to the shaft, with some angled pliers. I placed them into the gap in the circlip and prised the spring apart. With a bit of manipulation and dexterity it popped free.
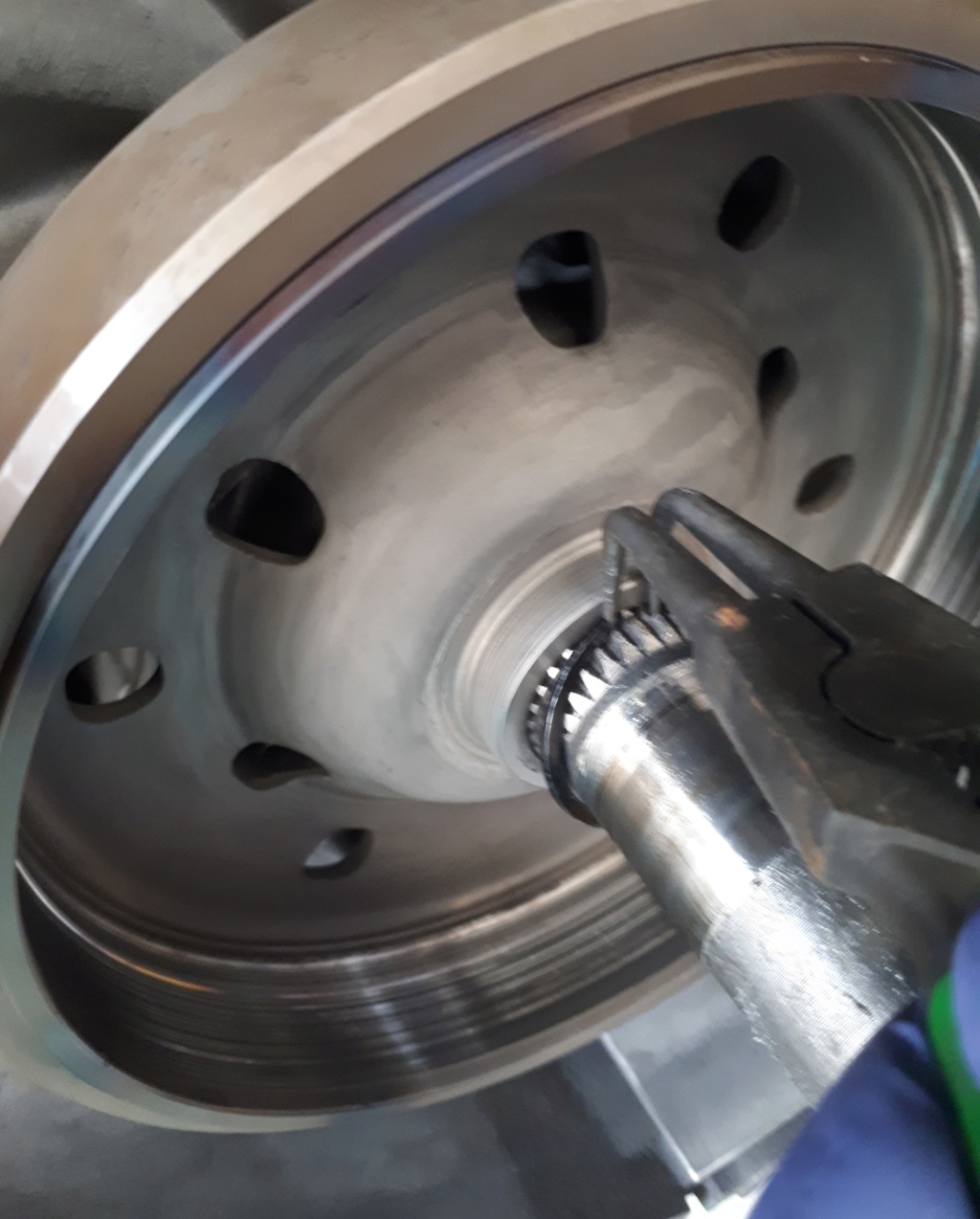
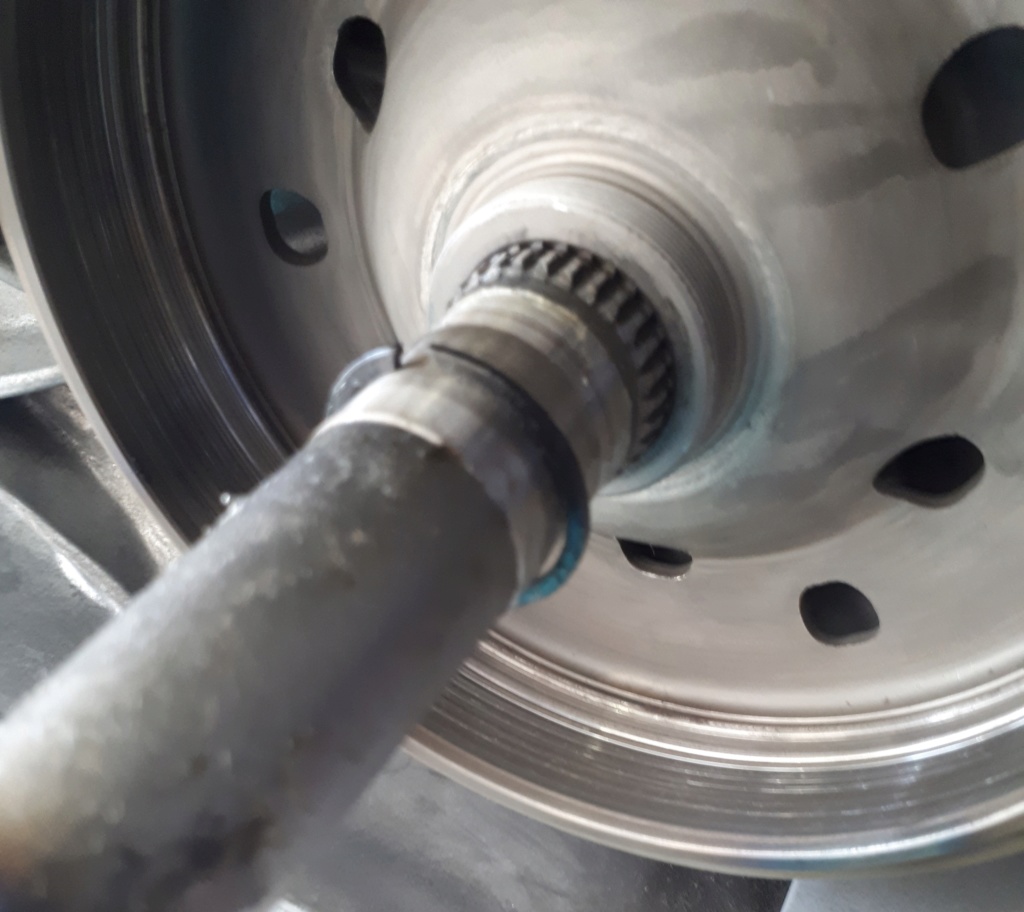
Next, the
puller. You can buy a long-legged
puller but I went down the cheap route. I bought a set of three different sized pullers, non of which would do the job. When dismantled and rebuilt, one of them could be made to fit.
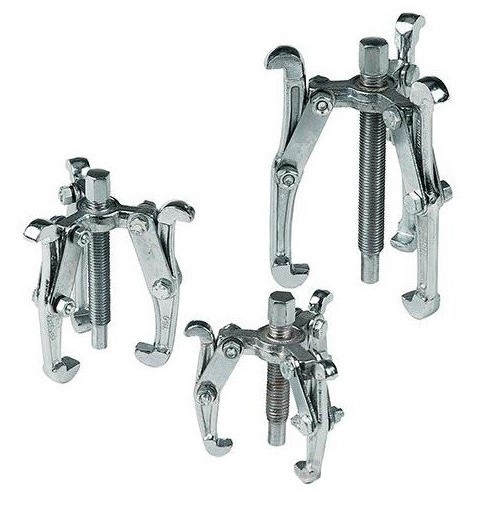
By using the largest
puller as the one to do the job I dismantled the other two so that I could use the 'legs' to extend the reach of the largest one.
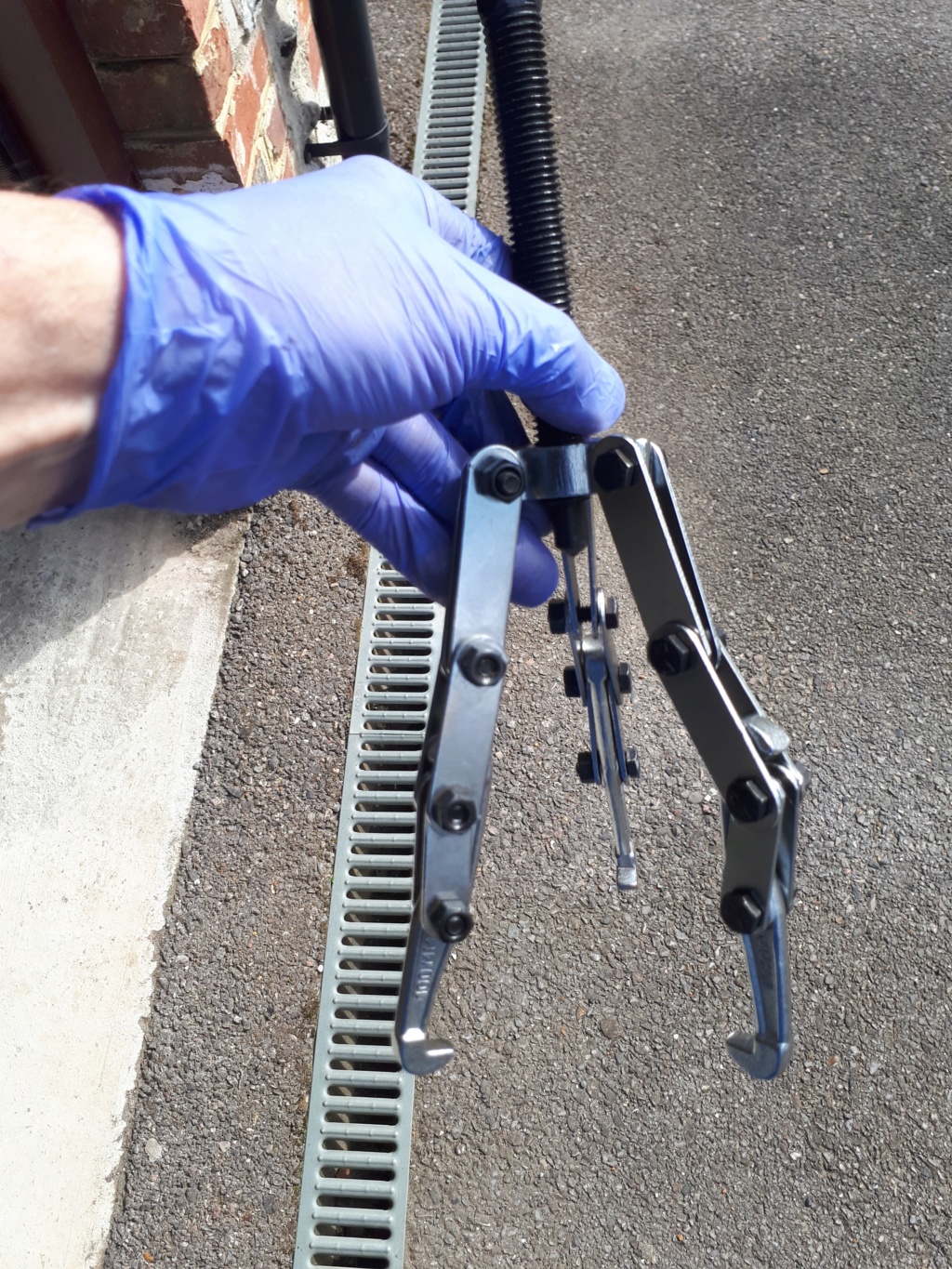
I attached the medium
puller's legs onto the largest
puller's legs and then attached the smallest
puller's legs to the medium
puller's legs, creating one long flexible set of legs. Then I attached the medium
puller's claws onto the end. The medium
puller's claws seem to fit the holes on the
clutch outer best.
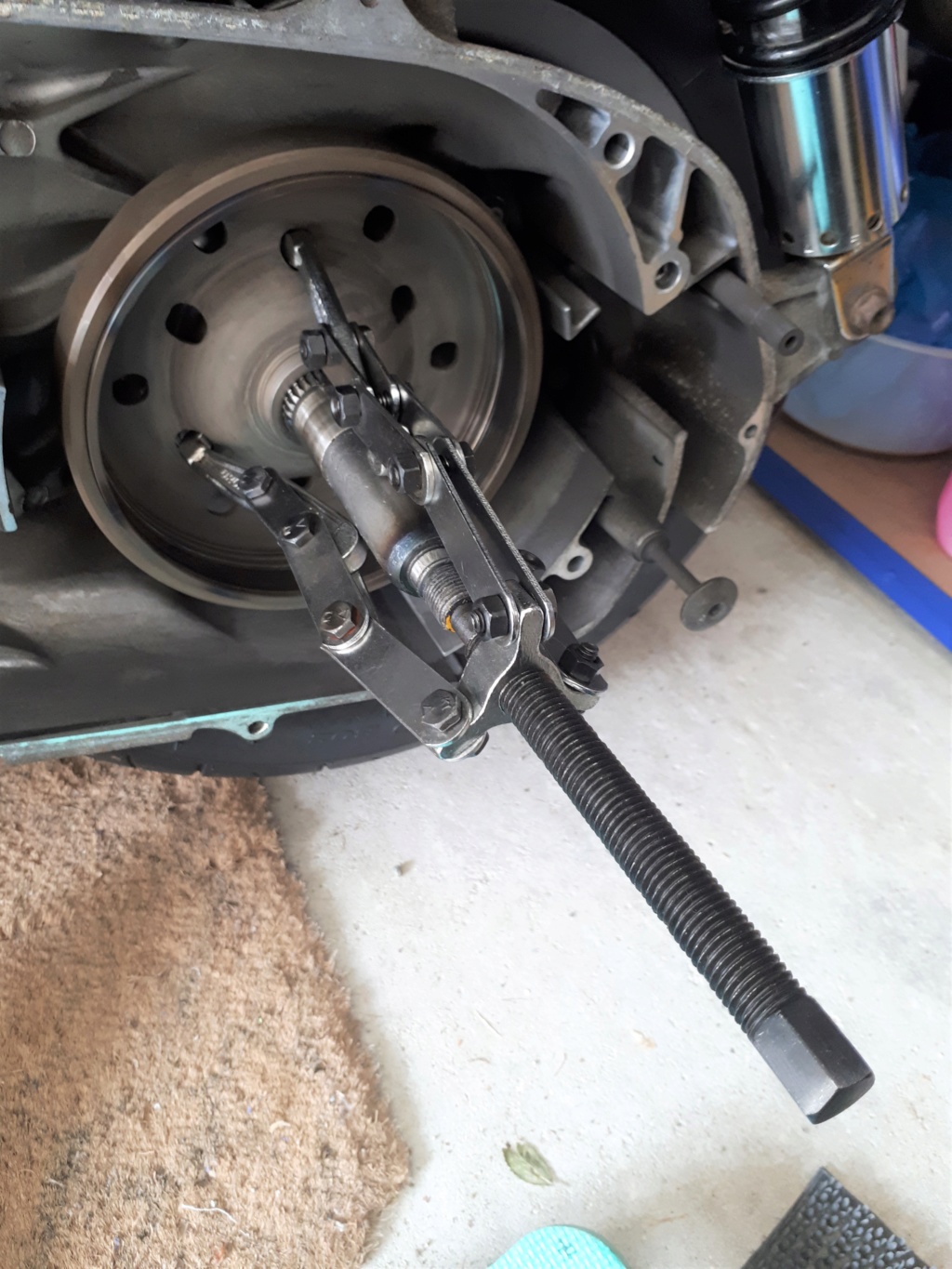
You might notice that the three claws do not go into equally spaced holes in the
clutch outer. Two fit into the inner holes and one claw has to go into one of the outer holes. This didn't affect the operation. (examine the picture).
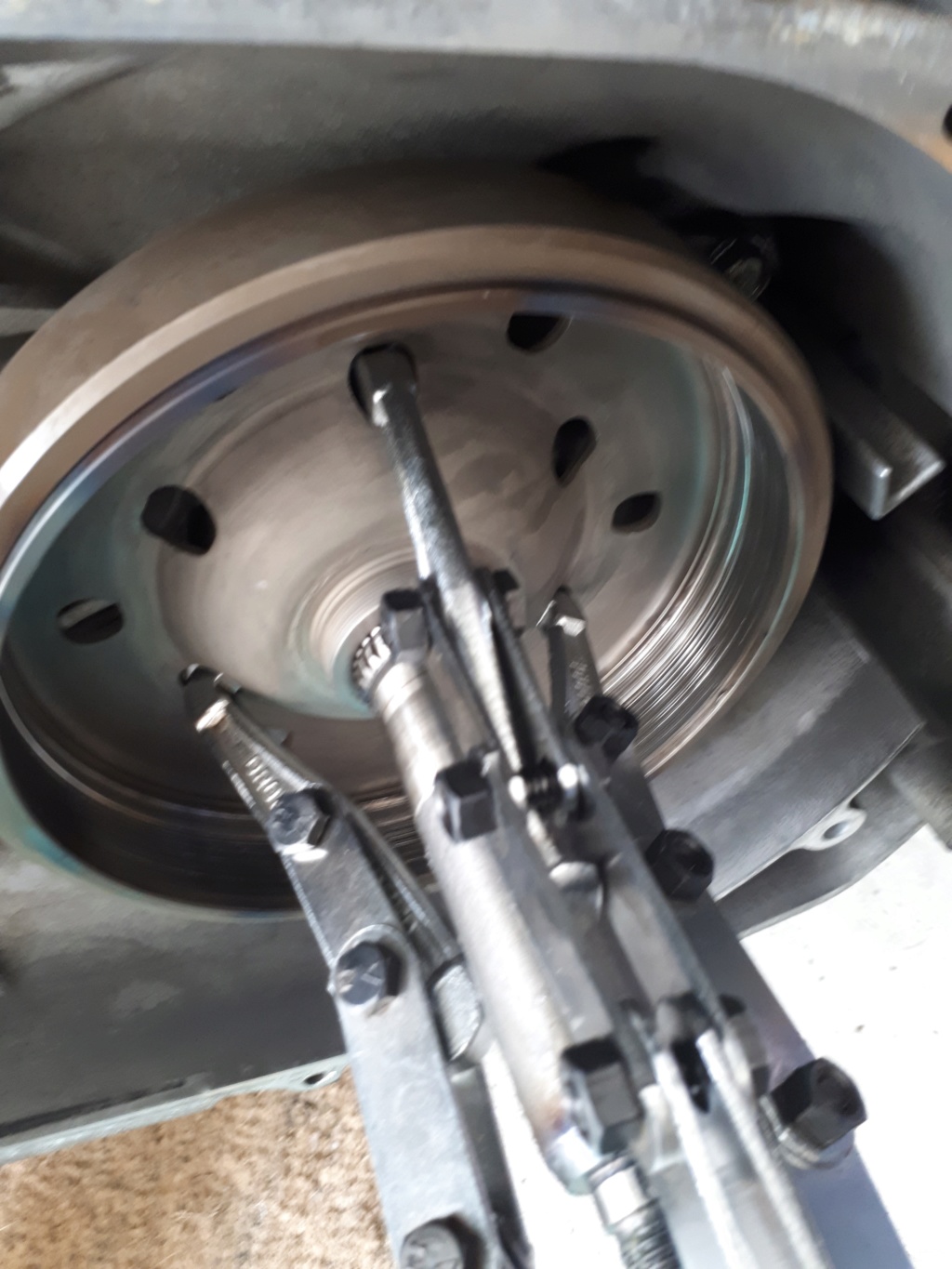
Start turning the nut ! There was a 'snap' as the outer broke free and then a creaking noise as is eased away from the splines. Then it was free...
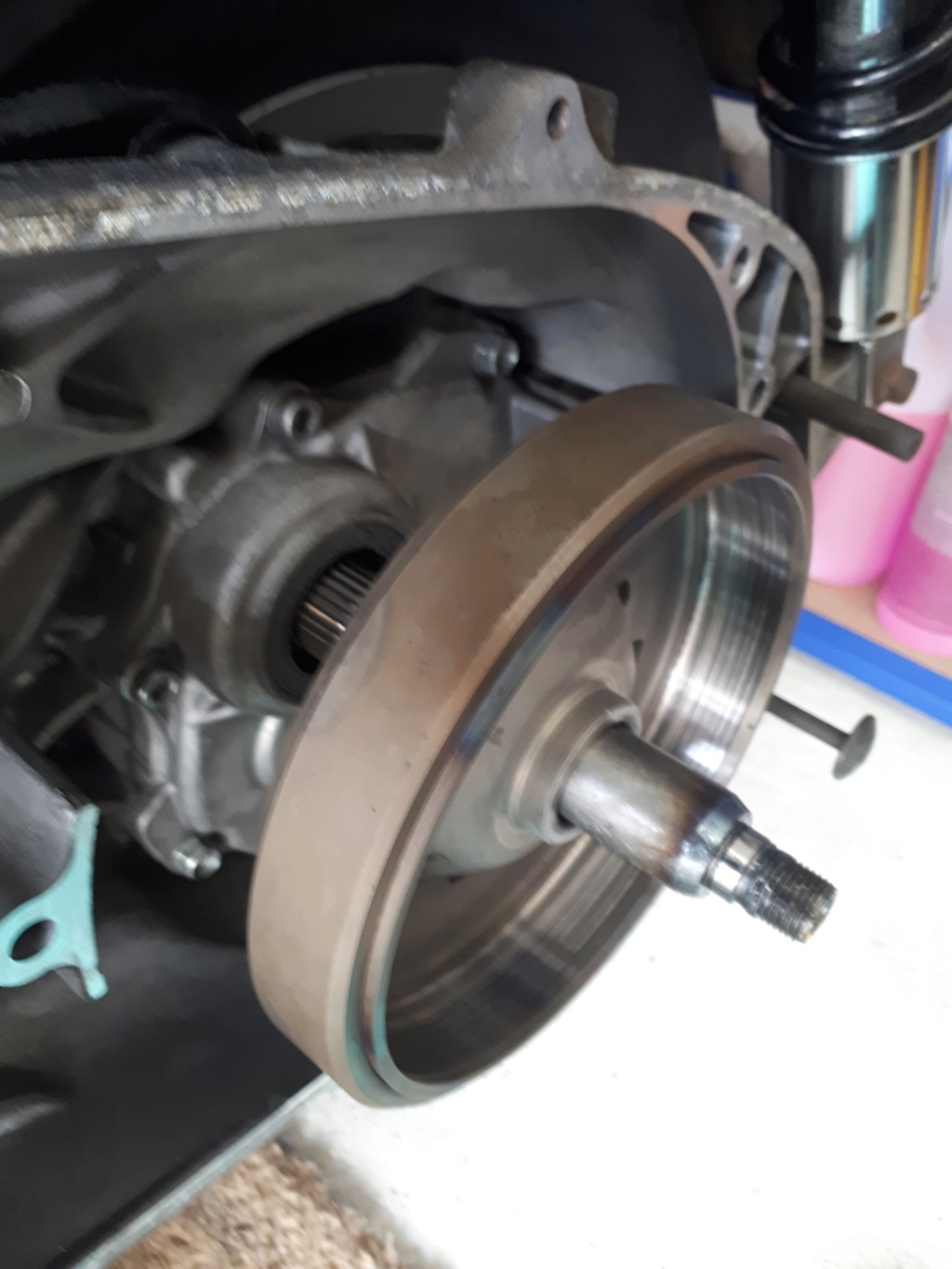
To replace the
clutch outer I used 1/12inch PVC pipe, cut squarely with a pipe cutter at 100mm, and M20 and M27 washers. By slightly enlarging the diameter of the inner surface at the end of the opening with a round file, I managed to 'screw' the pipe onto the threads of the
clutch outer, just as the Honda 'tool' would do. This seated nicely. Then I put on five M27 washers followed by four or five M20 washers and then fed on the shaft end-nut.
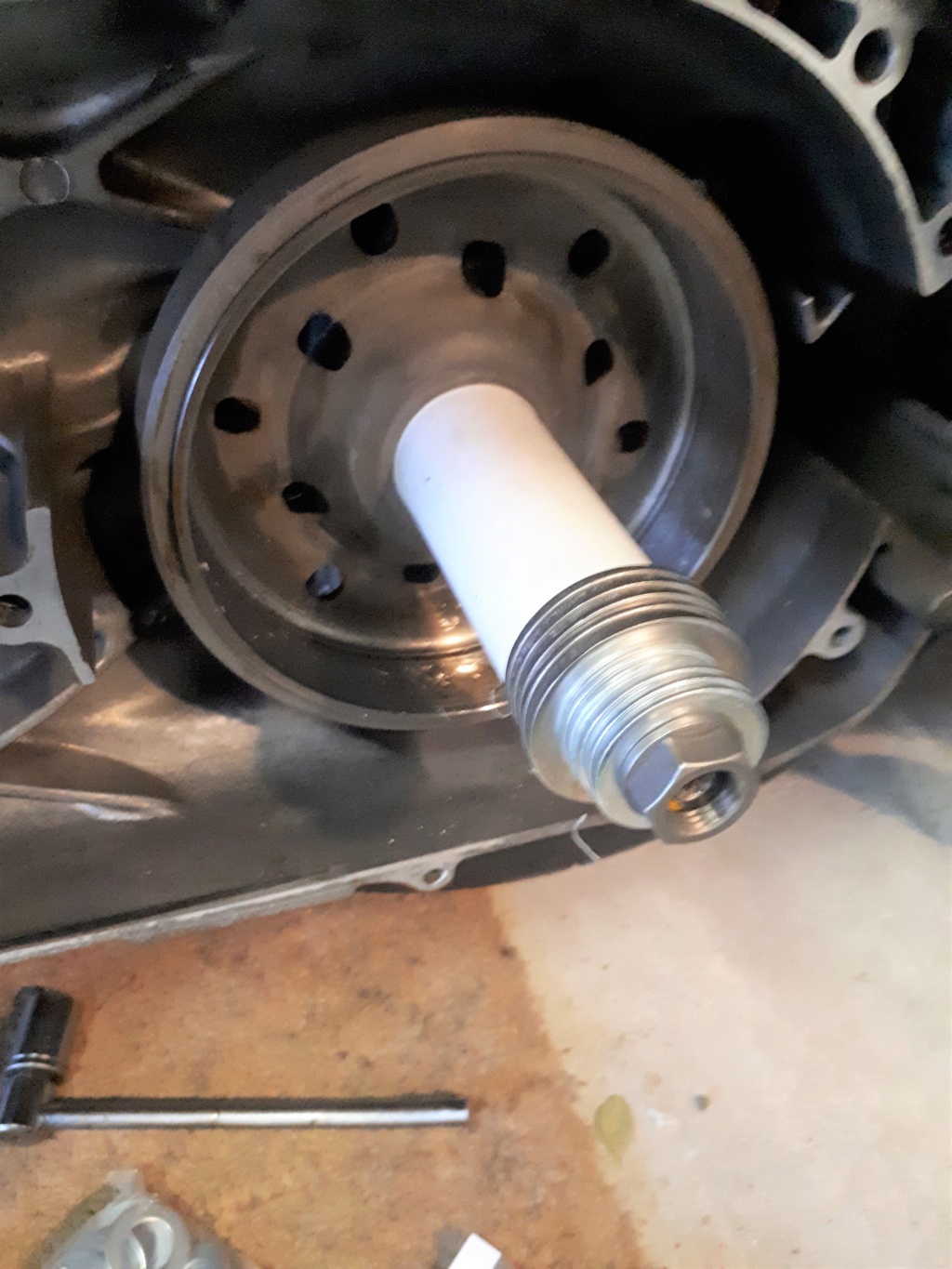
Start turning the nut and after about two turns, back off and remove the nut. Put on another M20 washer, put the nut on, and turn a bit more. Continue doing this after every couple of turns or so to make up the gap as you go. (make sure you don't run out of thread on the shaft). When you feel a firm resistance to your turning...stop. Remove the washers and pipe to see if the circlip groove is exposed. If not, give it another washer and tighten up again.
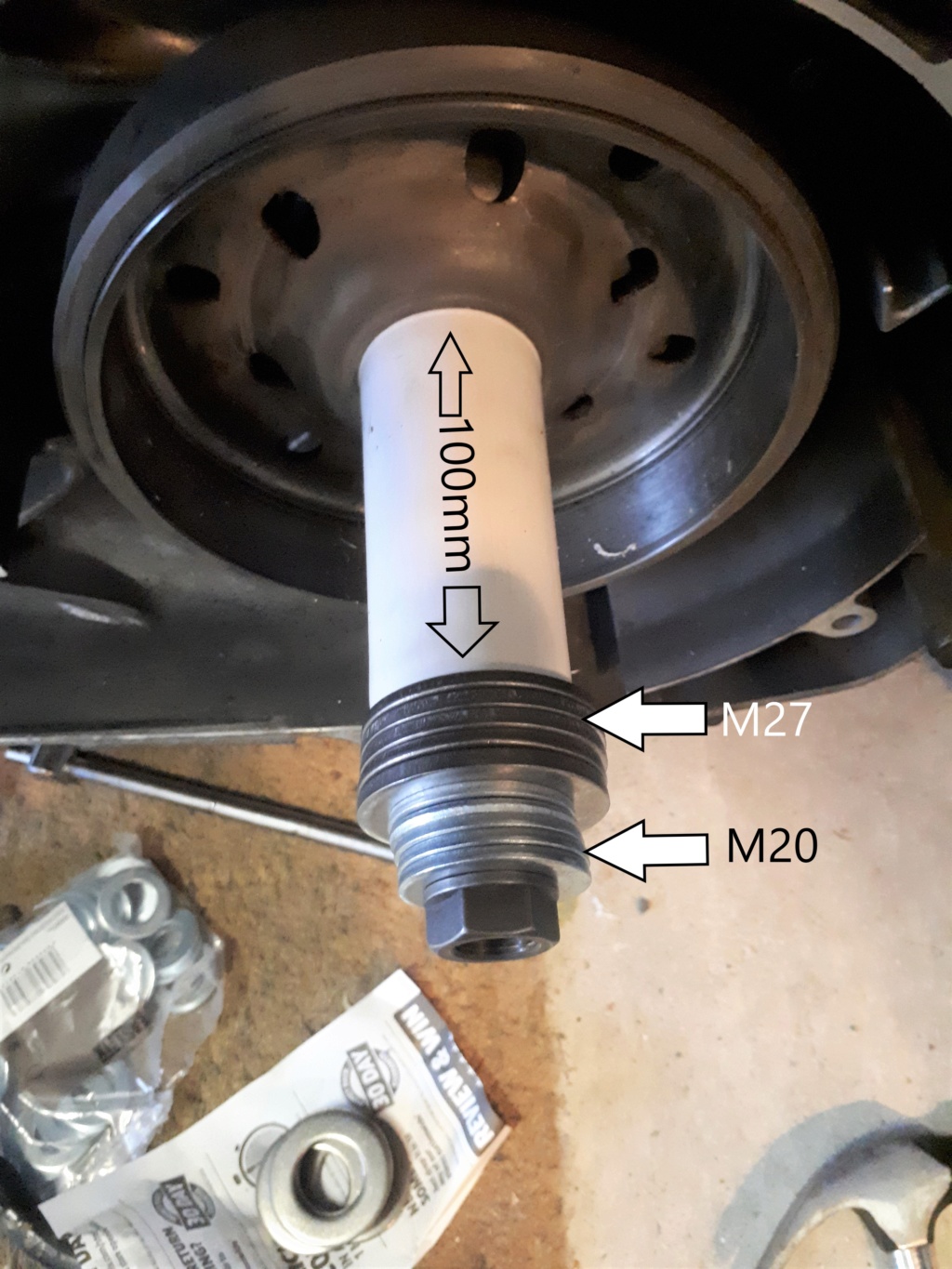
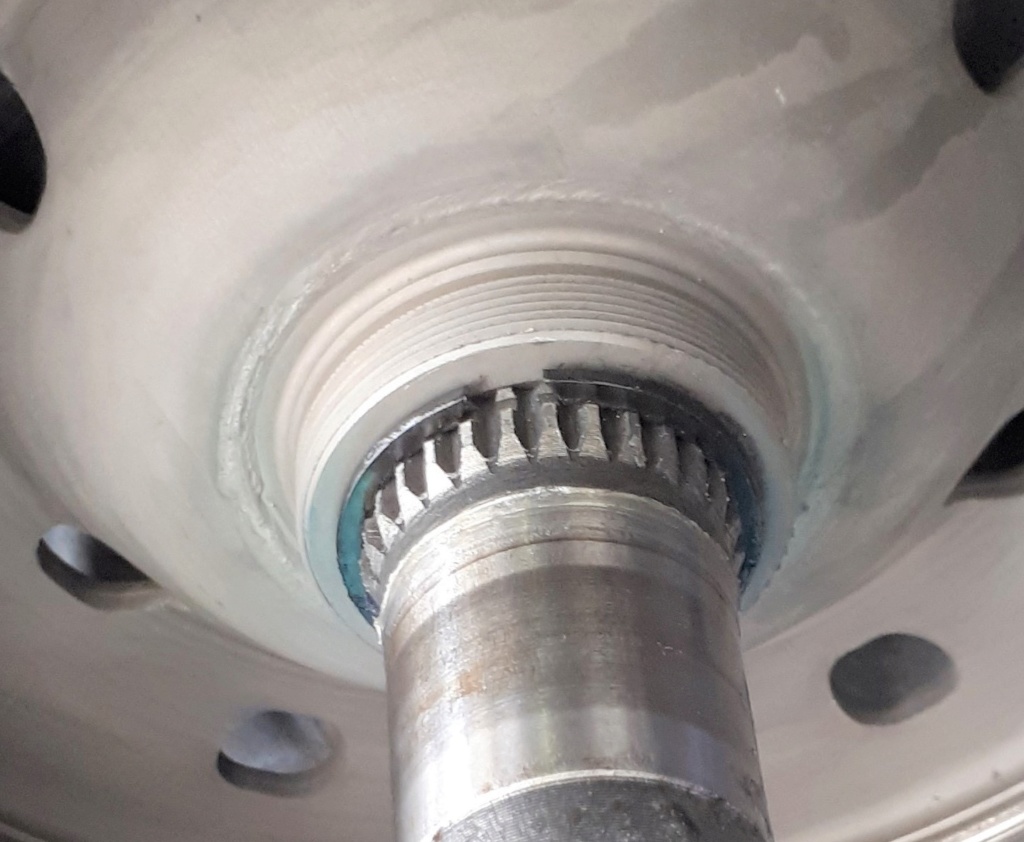
Once the circlip groove is exposed, you're almost there. Replace the circlip and check that it is seated neatly and squarely.
From here, you can replace the rest of the assembly (after some cleaning?). I hope this gives an idea of how easy this can be. Take your time, figure it out as you go and keep your piece of tube and the washers in a box for future use.
BTW, in case of confusion over washer sizes I include the dimensions:
M20 = Outside diameter of 37mm. Inside diameter of 21mm and thickness of 3mm.
M27 = Outside diameter of 50mm. Inside diameter of 28mm and thickness of 4mm.